TripleThreat719
Husqvarna
AA Class
Detailed writeup of my Lynx R Fairing and Headlight Upgrade with hyper links and pictures
So, up front, I should say that this will be a bit long…
Late last May, I picked up a used 2006 TE610 from my brother. The bike only had about 3500 miles on it and hadn’t been abused. However, it was a 10-year-old bike at the time I got it.
I had a cooling system failure on my first major ride in late August and ended up sticking the exhaust valves, which required a top end rebuild. While I had the bike torn down for that, I decided that I’d go on the search for some radiator guards and upgrade the anemic headlight.
I ultimately was able to locate a set of radiators and guards from a guy in Canada that I installed on the bike.
I settled on a new Lynx R fairing and headlight setup from Ian at Britiannia Composites. I ordered the standard light configuration and also opted for the GPS Mount Ian offers to have a nice place to mount the locking Touratech mount that would hold, protect and secure the Zumo. He even custom built it in matching husky blue.
It’s a really trick bit of kit and a well thought out design. Ian was awesome to work with and answered all my questions quickly and thoroughly.
While upgrading, I wanted to take advantage of the ability to set up the dash exactly the way I wanted, so I started planning all of the items I wanted to make sure I had in place.
Garmin Zumo 660 – I’ve been using this GPS for several years and really like it for turn-by-turn spoken directions with routes, Bluetooth connectivity with my cell phone, and Bluetooth connectivity with my SENA SMH10. I use the built-in MP3 Player on most rides and also use the SENA to communicate with my daughters or wife when they ride pillion, or a riding buddy when riding in a group.
Garmin GPSMap 60CSx – This little handheld GPS does a great job handling tracks and I frequently run it on the page with the compass when just out messing around not following tracks or a route on the Zumo.
A USB charging Port – This provides the ability to charge the SENA SMH10s while riding. Critical on a multi-day trip
A BMW Din Style Charging Port – a nice secure connection for any variety of additional accessories I may decide to add at some point down the road.
A Heated Gear power plug - Need a place to plug in my Warm-n-Safe heated jacket and pants.
A Volt gauge – Allows me to keep track of the charging system function when running a variety of accessories.
I needed a convenient way to power all of these accessories, so I decided to utilize the Rowe Electronics PDM60 Power Distribution Module. This is a completely programmable solution, capable of handling up to a 60 amp total power draw. It has 6 different circuits and each can be programmed for specific amperage limits, startup and shutdown delay times, as well as whether the circuit is activated by an ignition or ground trigger. It’s a really trick unit that eliminates fuses for each individual circuit because the device functions like a circuit breaker.
I have one circuit that I haven’t used yet, but I may eventually use it to provide power to my VIO POV Camera. I haven’t decided if I want to mount that to the bike, or wear it on my helmet and just use the existing BMW Din Power Port to provide external power to the camera. The other option is to use that extra circuit to power one of the new electric versions of a ScottOiler to increase chain and sprocket life.
The flexibility to set up the dash the way I wanted was limited by Husqvarna due to their incredibly short wiring harness connection to the main gauge cluster. It’s so short that the only option you would have would be to mount the gauge cluster at the very bottom of the dash, which I didn’t want to do.
As a result, I decided to build an extension for the stock harness. I sourced all of the parts from Digi-Key Electronics.
I started by selecting male and female plastic Molex connectors that matched the stock wiring harness and the pins that are crimped onto wires and then inserted into the plastic Molex connectors to create the functioning plug.
The connector that attaches to the stock wiring harness is called an 18 Position Rectangular Housing Connector Plug Natural 0.165" (4.20mm) and the Digi-Key Part Number is: WM1012-ND and the Molex Part Number is: 39-01-2181. Here is a photo:
The male connectors that get installed into the above referenced connector are called Contact Crimp Pin 18-24 AWG Tin and the Digi-Key Part Number is: WM2500-ND and the Molex Part Number is: 39-00-0041. Here is a photo:
The connector that attaches to the back of the Gauge Cluster is called an 18 Position Rectangular Housing Connector Receptacle Natural 0.165" (4.20mm) and the Digi-Key Part Number is: WM3708-ND and the Molex Part Number is: 39-01-2180. Here is a photo:
The female connectors that get installed into the above referenced connector are called Contact Crimp Socket 18-24 AWG Tin and the Digi-Key Part Number is: WM3116CT-ND and the Molex Part Number is: 0039000207. Here is a photo:
All of the connector parts cost me $11.31 shipped to my house and the 18 gauge wire was sourced from my local hardware store for a few dollars.
The most expensive part of building the extension was a quality Molex crimping tool. The durability of the extension depends on quality assembly of the individual wires that get inserted into the plastic connectors. Quality crimping is essential and a nice crimping tool is not cheap. I opted for the Molex 63811-1000 Service Grade Hand Crimping Tool and purchased it from Amazon for $56.08 at the time of this project. I’m certain I will use it again, so it was an investment in a quality tool that I will own and use many times in the future. Here is a photo:
Building the extension started with cutting enough pieces of wire to the desired length and stripping the ends. The extension doesn’t use every available spot in the 18 position connectors, so you only need 12 pieces of wire. Here is a picture of the end of the stock wiring harness where you can see that only 12 pins are utilized.
As you can see from the photo below, you only need to strip a very short piece of the insulation away from the ends of each wire in preparation to install the male and female connectors with the crimping tool.
Each of the pins has two sets of tabs that end up getting crimped. One set of tabs crimp to the stripped bare wire, and the other set end up getting crimped onto the insulation. The set that crimps into the insulation creates tensile strength in the connection by driving the ends of the tabs down into the insulation. As you can see (in the slightly blurry picture below) you insert the stripped wire into the pin so that the insulation of the wire is right up against the first set of tabs that get crimped onto the bare wire. And the second set are over the insulation.
The following picture gives you a better view of a male and female connector pins that have already been crimped. You can see that one set of tabs crimps onto the bare wire while the second set gets crimped into the insulation creating the tensile strength of the connector.
Once all of the wires have a male pin on one end and a female pin on the opposite end, you have to insert the pins into the plastic connectors. Make sure you put the correct pins in the correct plastic connector. They aren’t easy to get out, unless you have a special tool (which I didn’t buy).
You need to reference the original wiring harness to make sure that you are inserting the pins into the correct location in each of the plastic connectors. I then elected to cover the wires with a black plastic wire loom to make the harness less difficult to manage once installed on the bike.
I started by following the installation directions of the Lynx R fairing dash (which are well detailed and I won’t repeat here) and installing the GPS mount so I could begin mocking up the location of each component on the Lynx R dash. I started by covering it with masking tape to be able to lay out the location of all the items.
I started with laying out the location for the stock gauge cluster. Once I decided on the location, I used the stock gauge bracket to trace the location of the holes I needed to make. I used a small forstner bit in a portable cordless hand drill to establish the corners for the wiring harness hole as well as a standard twist drill to create the 3 mounting holes for the studs on the back of the gauge cluster.
The next step was to place the stock gauge cluster into position and lay out the locations for the USB Charging Port, Volt Gauge, and BMW Style Din Charging Port.
I then used a 1-1/8” forstner bit to drill the holes for each of those three items.
I selected the right side wing of the dash for the installation location for the stock ignition key unit and used a rotozip tool to cut the appropriately shaped hole (a circle with one flat section that prevents the ignition key unit from twisting in the hole as you turn the key).
After removing all of the masking tape, I then assembled all of the items into the dash and had the first look at how it all would come together on the finished dash.
So, up front, I should say that this will be a bit long…
Late last May, I picked up a used 2006 TE610 from my brother. The bike only had about 3500 miles on it and hadn’t been abused. However, it was a 10-year-old bike at the time I got it.
I had a cooling system failure on my first major ride in late August and ended up sticking the exhaust valves, which required a top end rebuild. While I had the bike torn down for that, I decided that I’d go on the search for some radiator guards and upgrade the anemic headlight.
I ultimately was able to locate a set of radiators and guards from a guy in Canada that I installed on the bike.

I settled on a new Lynx R fairing and headlight setup from Ian at Britiannia Composites. I ordered the standard light configuration and also opted for the GPS Mount Ian offers to have a nice place to mount the locking Touratech mount that would hold, protect and secure the Zumo. He even custom built it in matching husky blue.
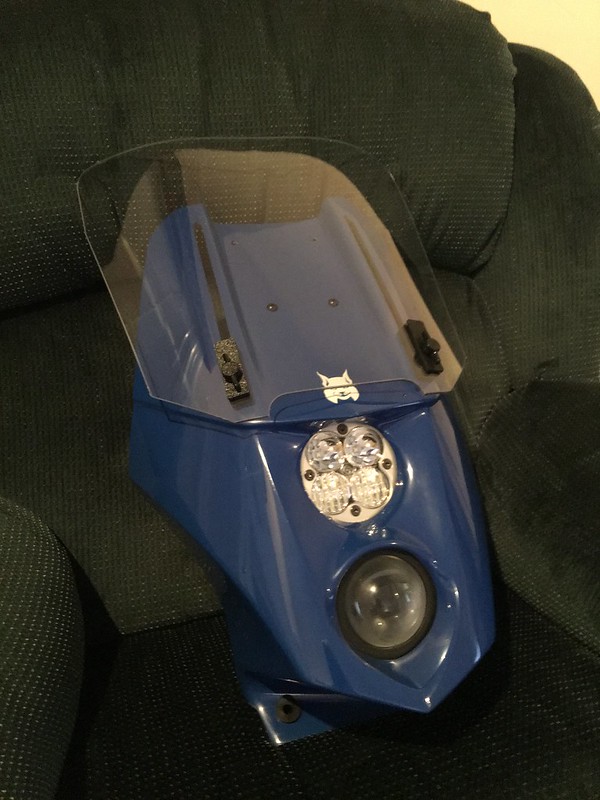
It’s a really trick bit of kit and a well thought out design. Ian was awesome to work with and answered all my questions quickly and thoroughly.
While upgrading, I wanted to take advantage of the ability to set up the dash exactly the way I wanted, so I started planning all of the items I wanted to make sure I had in place.
Garmin Zumo 660 – I’ve been using this GPS for several years and really like it for turn-by-turn spoken directions with routes, Bluetooth connectivity with my cell phone, and Bluetooth connectivity with my SENA SMH10. I use the built-in MP3 Player on most rides and also use the SENA to communicate with my daughters or wife when they ride pillion, or a riding buddy when riding in a group.
Garmin GPSMap 60CSx – This little handheld GPS does a great job handling tracks and I frequently run it on the page with the compass when just out messing around not following tracks or a route on the Zumo.
A USB charging Port – This provides the ability to charge the SENA SMH10s while riding. Critical on a multi-day trip
A BMW Din Style Charging Port – a nice secure connection for any variety of additional accessories I may decide to add at some point down the road.
A Heated Gear power plug - Need a place to plug in my Warm-n-Safe heated jacket and pants.
A Volt gauge – Allows me to keep track of the charging system function when running a variety of accessories.
I needed a convenient way to power all of these accessories, so I decided to utilize the Rowe Electronics PDM60 Power Distribution Module. This is a completely programmable solution, capable of handling up to a 60 amp total power draw. It has 6 different circuits and each can be programmed for specific amperage limits, startup and shutdown delay times, as well as whether the circuit is activated by an ignition or ground trigger. It’s a really trick unit that eliminates fuses for each individual circuit because the device functions like a circuit breaker.
I have one circuit that I haven’t used yet, but I may eventually use it to provide power to my VIO POV Camera. I haven’t decided if I want to mount that to the bike, or wear it on my helmet and just use the existing BMW Din Power Port to provide external power to the camera. The other option is to use that extra circuit to power one of the new electric versions of a ScottOiler to increase chain and sprocket life.
The flexibility to set up the dash the way I wanted was limited by Husqvarna due to their incredibly short wiring harness connection to the main gauge cluster. It’s so short that the only option you would have would be to mount the gauge cluster at the very bottom of the dash, which I didn’t want to do.
As a result, I decided to build an extension for the stock harness. I sourced all of the parts from Digi-Key Electronics.
I started by selecting male and female plastic Molex connectors that matched the stock wiring harness and the pins that are crimped onto wires and then inserted into the plastic Molex connectors to create the functioning plug.
The connector that attaches to the stock wiring harness is called an 18 Position Rectangular Housing Connector Plug Natural 0.165" (4.20mm) and the Digi-Key Part Number is: WM1012-ND and the Molex Part Number is: 39-01-2181. Here is a photo:
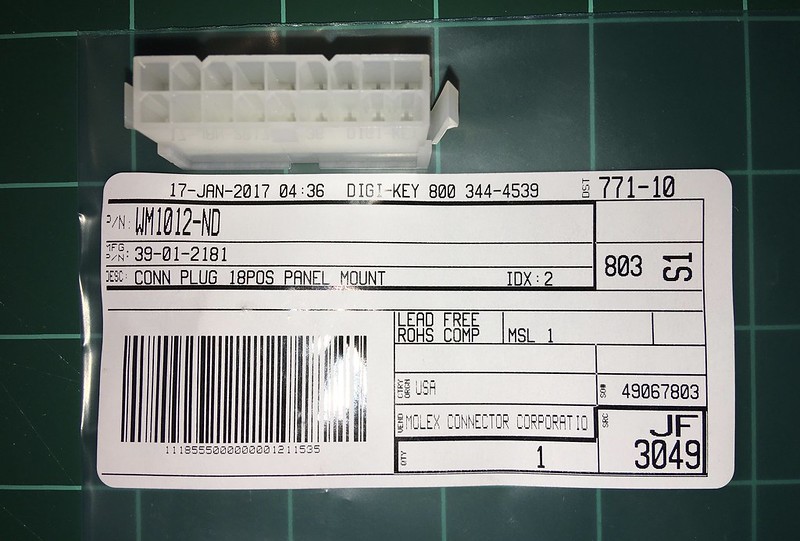
The male connectors that get installed into the above referenced connector are called Contact Crimp Pin 18-24 AWG Tin and the Digi-Key Part Number is: WM2500-ND and the Molex Part Number is: 39-00-0041. Here is a photo:
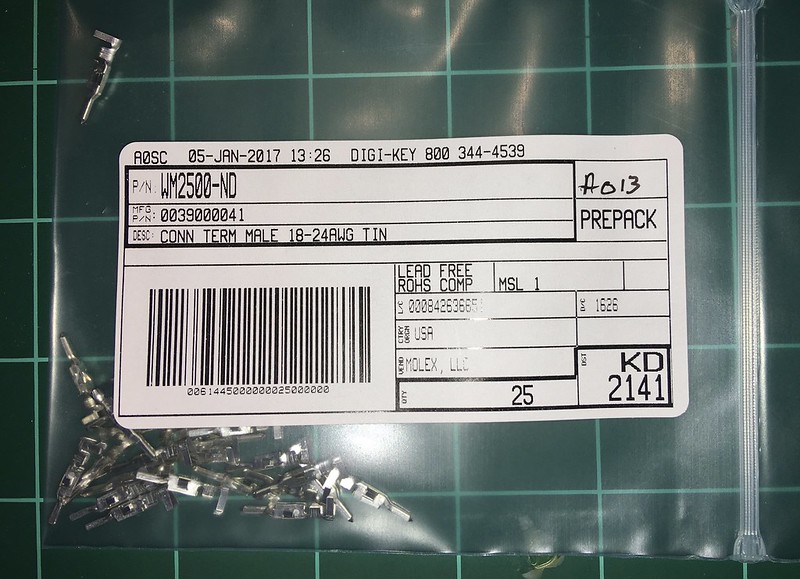
The connector that attaches to the back of the Gauge Cluster is called an 18 Position Rectangular Housing Connector Receptacle Natural 0.165" (4.20mm) and the Digi-Key Part Number is: WM3708-ND and the Molex Part Number is: 39-01-2180. Here is a photo:
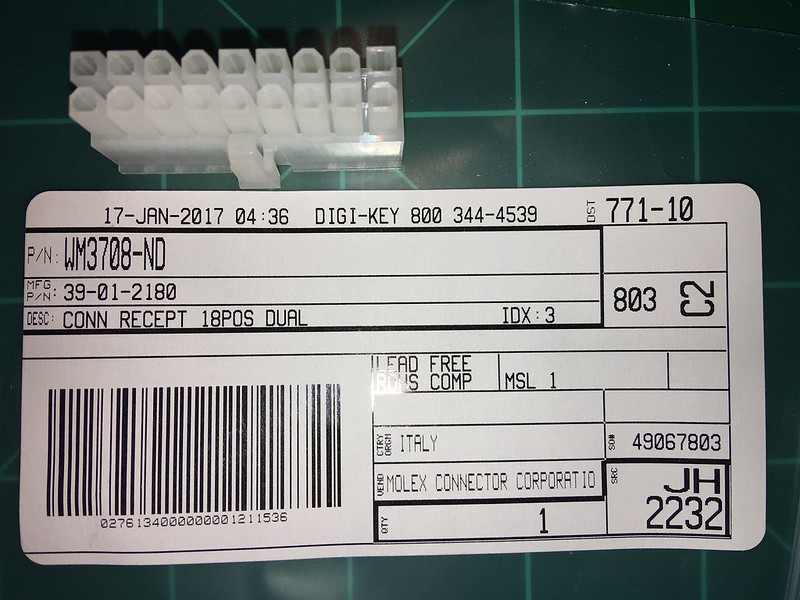
The female connectors that get installed into the above referenced connector are called Contact Crimp Socket 18-24 AWG Tin and the Digi-Key Part Number is: WM3116CT-ND and the Molex Part Number is: 0039000207. Here is a photo:
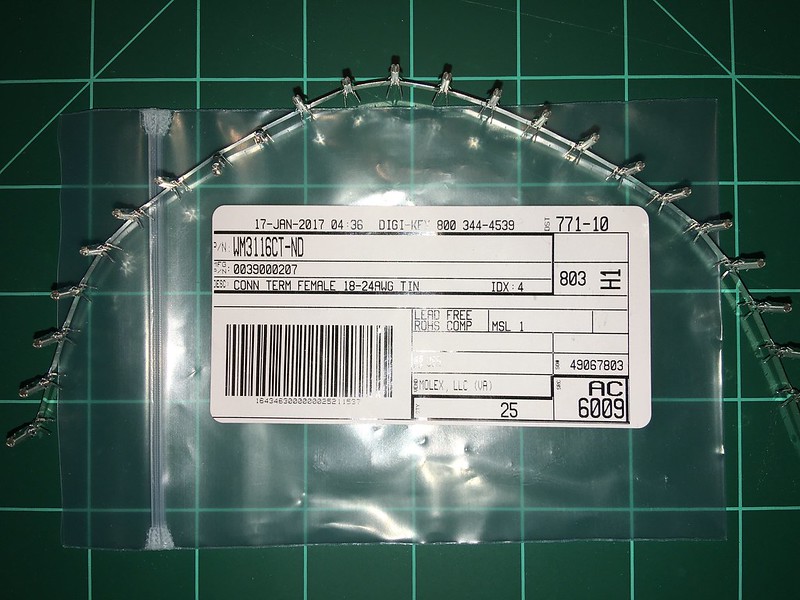
All of the connector parts cost me $11.31 shipped to my house and the 18 gauge wire was sourced from my local hardware store for a few dollars.
The most expensive part of building the extension was a quality Molex crimping tool. The durability of the extension depends on quality assembly of the individual wires that get inserted into the plastic connectors. Quality crimping is essential and a nice crimping tool is not cheap. I opted for the Molex 63811-1000 Service Grade Hand Crimping Tool and purchased it from Amazon for $56.08 at the time of this project. I’m certain I will use it again, so it was an investment in a quality tool that I will own and use many times in the future. Here is a photo:

Building the extension started with cutting enough pieces of wire to the desired length and stripping the ends. The extension doesn’t use every available spot in the 18 position connectors, so you only need 12 pieces of wire. Here is a picture of the end of the stock wiring harness where you can see that only 12 pins are utilized.
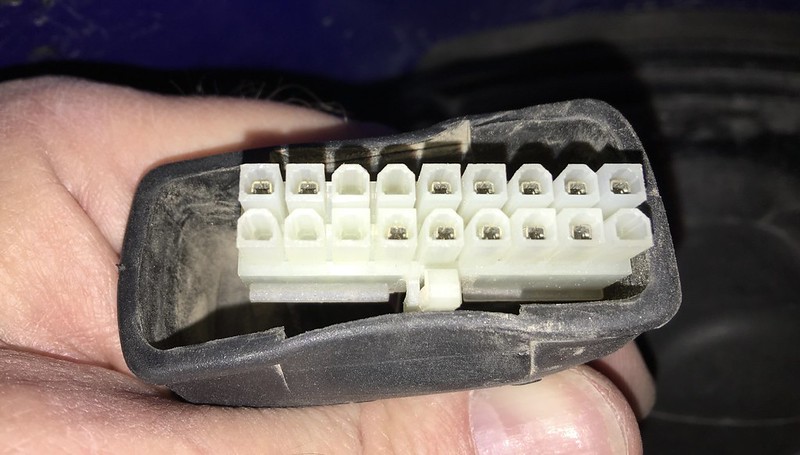
As you can see from the photo below, you only need to strip a very short piece of the insulation away from the ends of each wire in preparation to install the male and female connectors with the crimping tool.
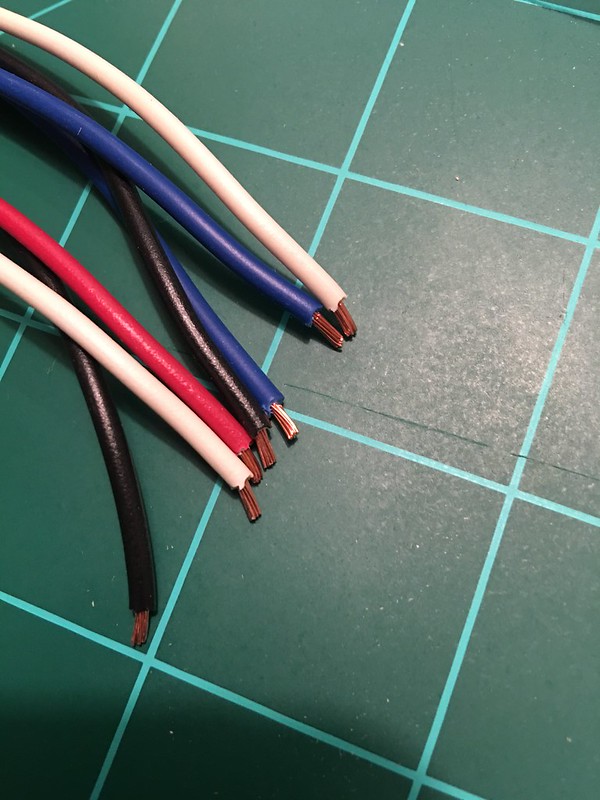
Each of the pins has two sets of tabs that end up getting crimped. One set of tabs crimp to the stripped bare wire, and the other set end up getting crimped onto the insulation. The set that crimps into the insulation creates tensile strength in the connection by driving the ends of the tabs down into the insulation. As you can see (in the slightly blurry picture below) you insert the stripped wire into the pin so that the insulation of the wire is right up against the first set of tabs that get crimped onto the bare wire. And the second set are over the insulation.
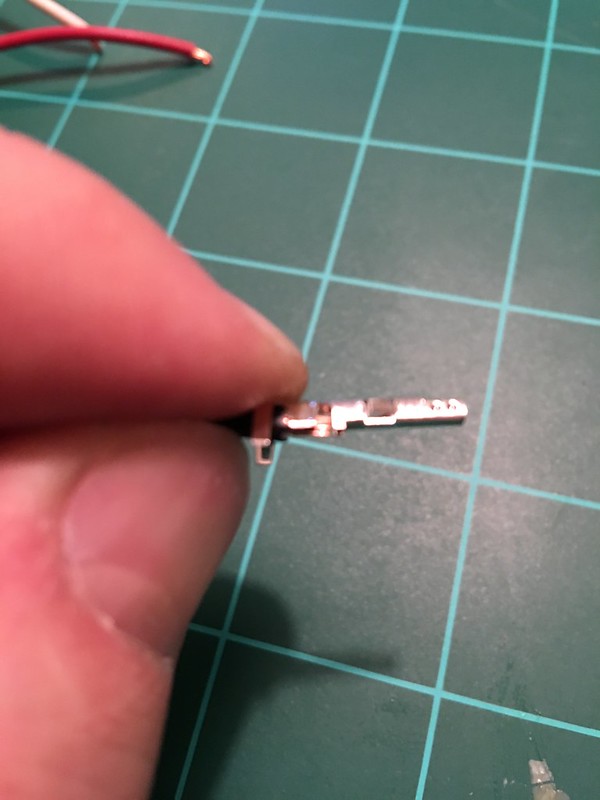
The following picture gives you a better view of a male and female connector pins that have already been crimped. You can see that one set of tabs crimps onto the bare wire while the second set gets crimped into the insulation creating the tensile strength of the connector.
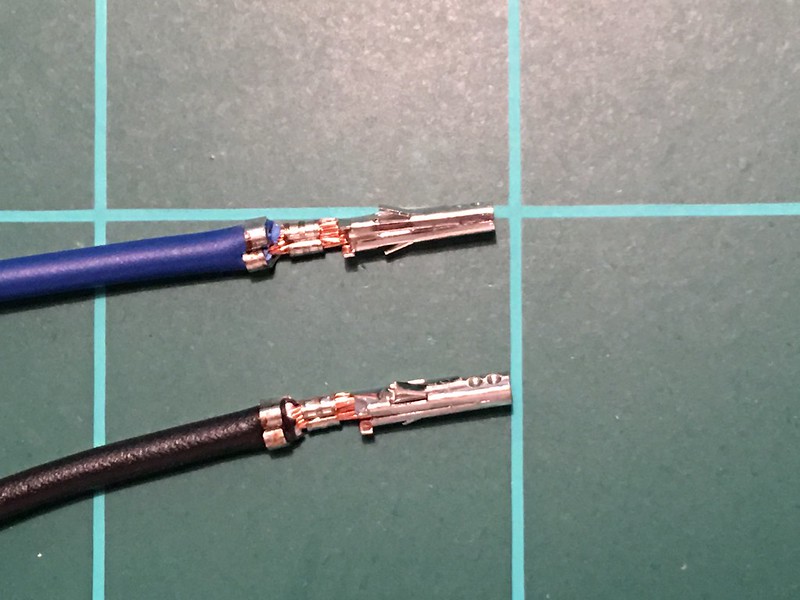
Once all of the wires have a male pin on one end and a female pin on the opposite end, you have to insert the pins into the plastic connectors. Make sure you put the correct pins in the correct plastic connector. They aren’t easy to get out, unless you have a special tool (which I didn’t buy).
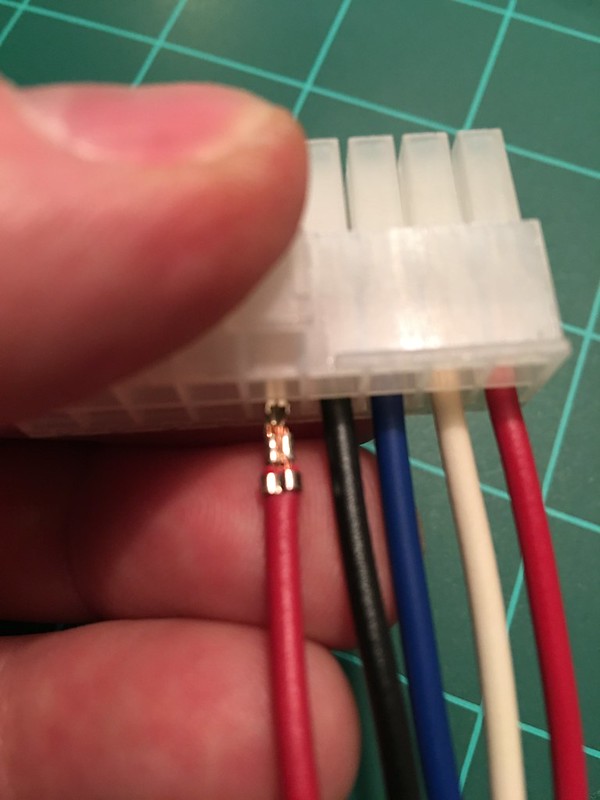
You need to reference the original wiring harness to make sure that you are inserting the pins into the correct location in each of the plastic connectors. I then elected to cover the wires with a black plastic wire loom to make the harness less difficult to manage once installed on the bike.
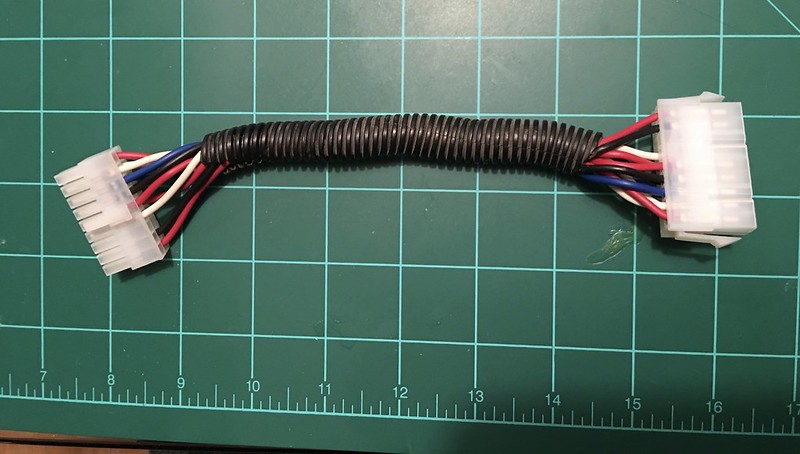
I started by following the installation directions of the Lynx R fairing dash (which are well detailed and I won’t repeat here) and installing the GPS mount so I could begin mocking up the location of each component on the Lynx R dash. I started by covering it with masking tape to be able to lay out the location of all the items.
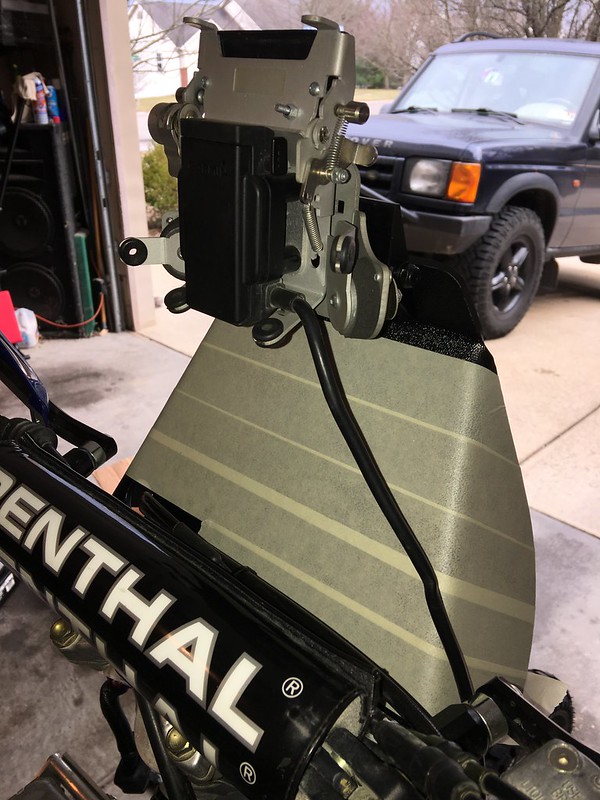
I started with laying out the location for the stock gauge cluster. Once I decided on the location, I used the stock gauge bracket to trace the location of the holes I needed to make. I used a small forstner bit in a portable cordless hand drill to establish the corners for the wiring harness hole as well as a standard twist drill to create the 3 mounting holes for the studs on the back of the gauge cluster.
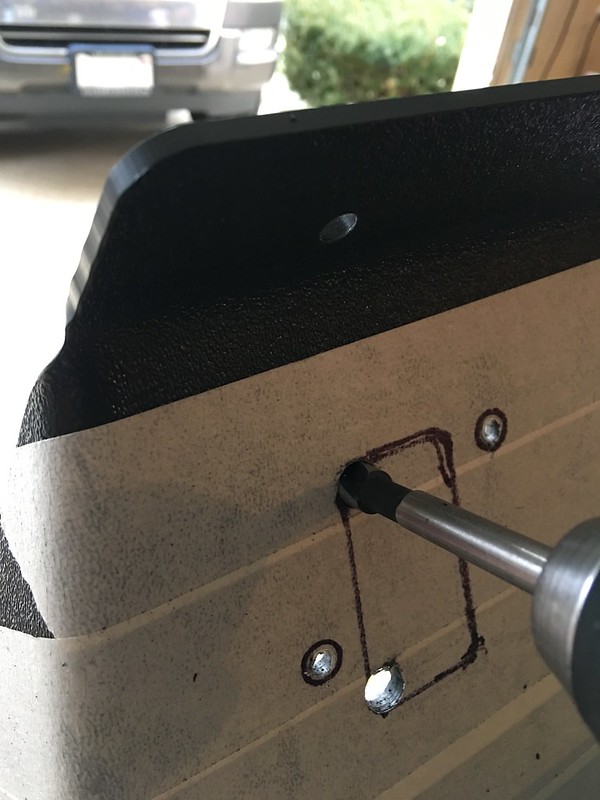
The next step was to place the stock gauge cluster into position and lay out the locations for the USB Charging Port, Volt Gauge, and BMW Style Din Charging Port.
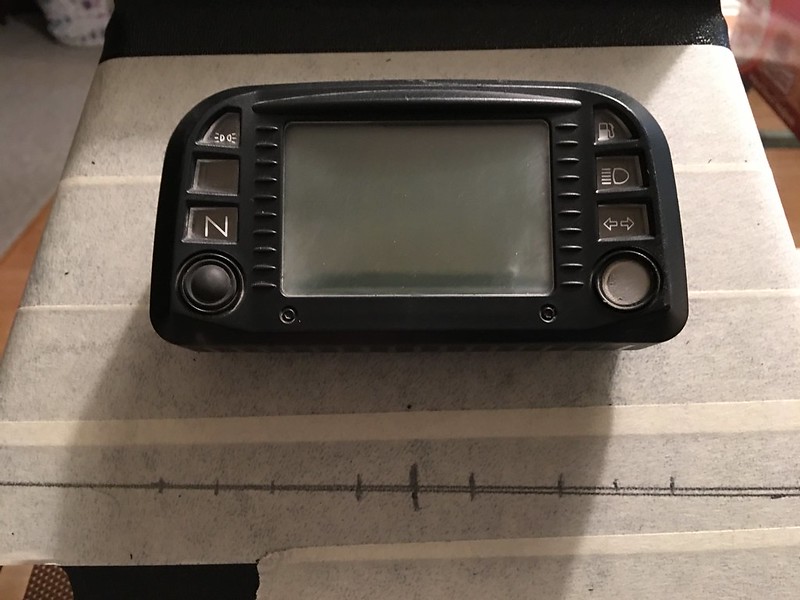
I then used a 1-1/8” forstner bit to drill the holes for each of those three items.
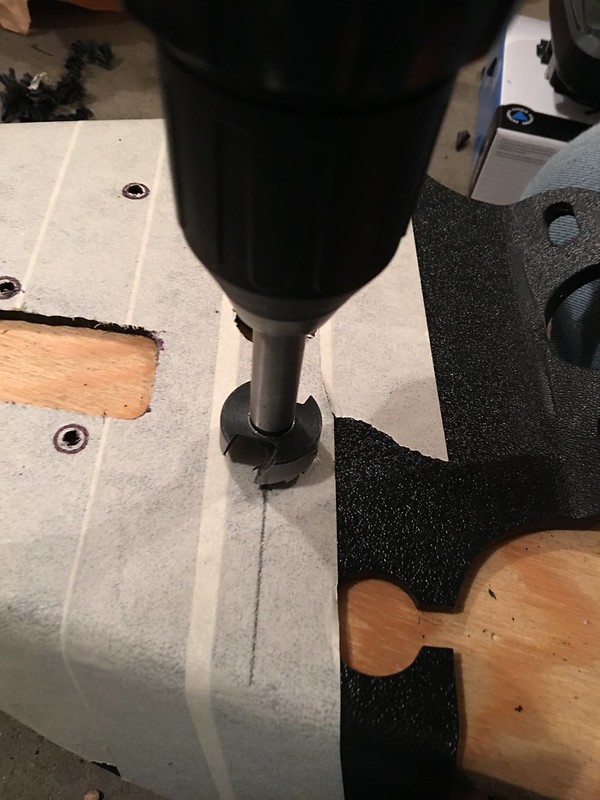
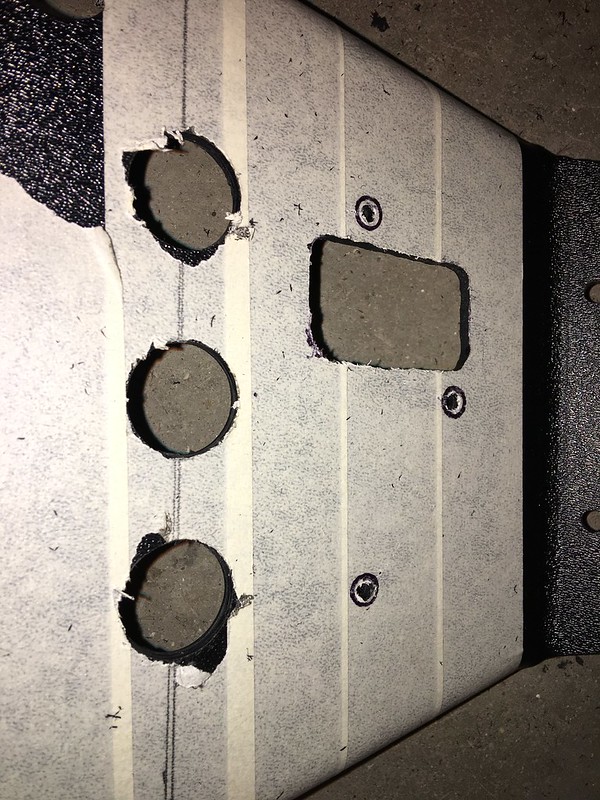
I selected the right side wing of the dash for the installation location for the stock ignition key unit and used a rotozip tool to cut the appropriately shaped hole (a circle with one flat section that prevents the ignition key unit from twisting in the hole as you turn the key).
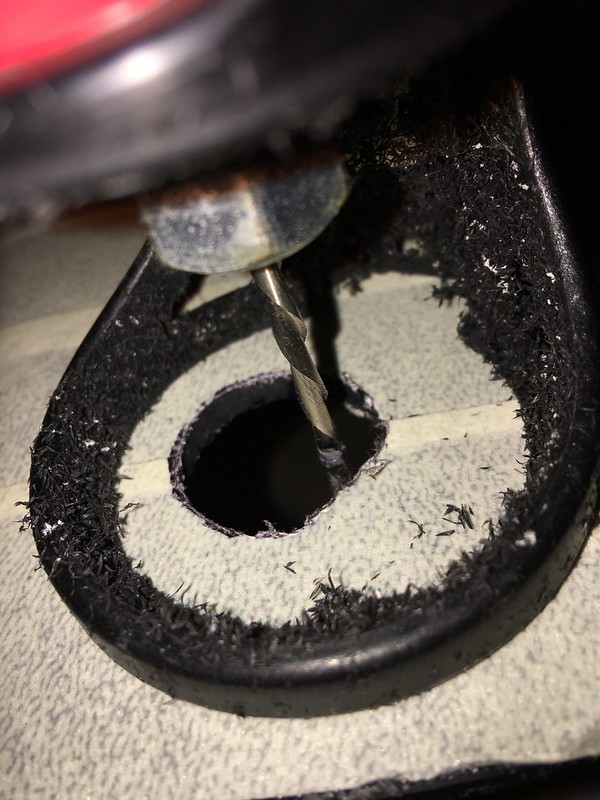
After removing all of the masking tape, I then assembled all of the items into the dash and had the first look at how it all would come together on the finished dash.
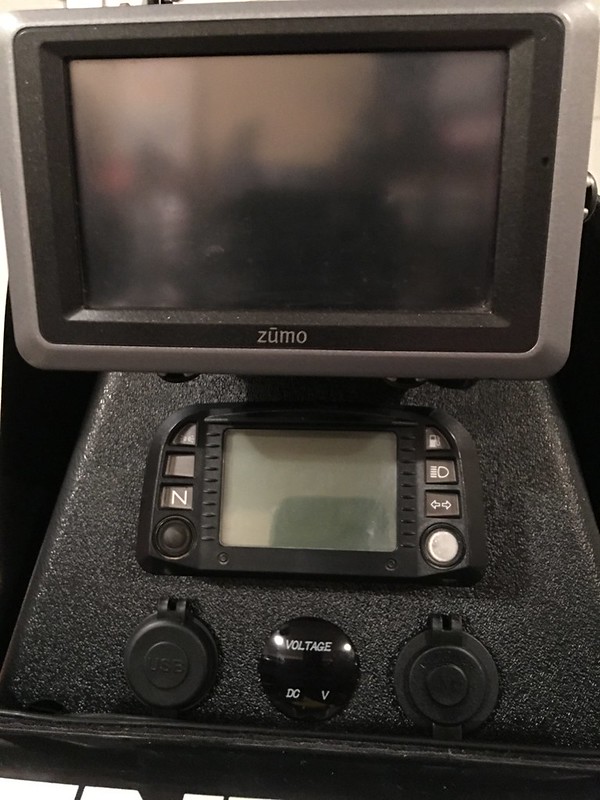