So here’s the photos of the big bits after cleaning and coating. My comments so far are:
Strip issues
1. Pulled wrong half of crankcase off crank when spitting cases, would have been OK but left oil/breather ? tube in back of cases which stopped them splitting. Removed tube, split cases. Guess it doesn’t matter to much.
2. Both main bearings stayed on crank, not in cases. Seems interference fit of the inner race is much tighter on shaft than the outer race in the case?
3. Getting bearings off the crank is hard, no space for bearing splitters (and you need a big one to make the span). Resorted to using small metal wedge (engineers chisel....) to move the bearings the first 5mm. Not nice but any one know a better way ? Bearing splitter then could get under the outer race for the next 20mm. Still not free from crank, so used bearing puller onto the splitter to go the rest of the way.
4. Once off I could clean up the lands on the crankshaft then found bearings still tight but easier, and would go into the case half with Tusk crankshaft puller (but only on one side). But still much tighter than the bearing fit in crankcase with everything at room temp.
5. So will try putting new bearings on crank first. Experimented assembly with old bearings to see what looked easiest. Found that if bearings heated with hot air gun then bearing would drop easily by gravity onto cold crankshaft (even without chilling the crank). This seems the easiest way without any excessive force or resorting to any pullers or drifts etc.
6. Then did test assembly of crank halves on to crank with mains fitted but no seals. If crankcase is heated with hot air gun then crank just drops in both sides.
7. Unlike left kickers crankcase halves are not gasketted. Struggled to source yamabond in UK (WHY !) so have got hold of HondaBond. I wonder if there is HuskyBond.....
8. No shims seem to fitted on the crank inboard of the mains? Assume this is because the cases are metal to metal so gap is controlled.
9. Let’s hope I can get the seals in after the cases are together.
10. On stripping all the loose parts out of the cases prior to cleaning I managed to snap off my fancy new Allen bolt 3/8 waisted keys in one of the bolts. They were all really tight and seemed assembled with loctite. So plenty of heat and anti seize used. But getting the broken bit of Allen key out was a complete pain. Ended up dremmeling (is that a new verb) a slot into the whole countersunk screw broken key and all. Then biggest slot driver in my trusty impact wrench. Good way of wasting a few hours...
11. I use a local company to aquablast the cases but beware. The process uses a rock hard abrasive paste and whilst cleans a treat, any small particles left in will come out in the assembled engine and wreak holiday in your new motor. So, blast out with air, put in wash tank, soak overnight, blast out and repeat until your absolutely sure it’s clean. Then spray the cases with preserving oil. My mate still won’t trust aquablast after wrecking a newly rebuilt motor and only uses a pure water jetting process. It must use very high pressure because it works real well, but can be expensive.
12. Bearings. I replace all the ball bearings regardless as they are cheap. But replace the roller bearings on a condition basis. I clean them in an ultrasonic bath , apply light oil and listen when spun. If not totally smooth and quiet they get changed. Why, because I think may be expensive and hard to source (long lead times). At least that what my bearing shop said, anyone know where to get the roller bearings without paying Husky/bike shop prices ?
Next post, getting the cases together (hopefully)
DM
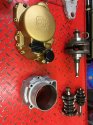