dartyppyt
Husqvarna
Pro Class
Last but not least, I take a permanent marker and write on my left lower fork,axle pinch clamp. The permanent fork reading from point to point or punch to punch mark.
Go ahead and reassemble everything. From now on when you remove your front wheel. All you have to do is feed your tool thru your rotor, set it from point to point at 186 mm and you have perfect fork alignment with no binding.
Note: On the newer Braking rotors you can feed the tool in without removing an end. On the older style rotors, you have to use a little finesse by taking one end off your tool and feeding it thru the spokes/rotors. I took a picture of my old tool but it is not on my camera. I will post it in the next few days that works easier on the old rotors.
So, you can bounce, compress, do what ever you prefer. But I learned along time ago that it didn't work for accuracy/less stiction. Try doing it this way once, then try the bounce, brake and compress method and see how far you are off.
Out of curiosity, my son's 08 WR 125, with the bounce, brake and compress method. It was 2mm off. It sure made a difference in the stiction free up only being off 2 mm. Being off like that has to take it's toll on the bushings and seals.
Go ahead and reassemble everything. From now on when you remove your front wheel. All you have to do is feed your tool thru your rotor, set it from point to point at 186 mm and you have perfect fork alignment with no binding.
Note: On the newer Braking rotors you can feed the tool in without removing an end. On the older style rotors, you have to use a little finesse by taking one end off your tool and feeding it thru the spokes/rotors. I took a picture of my old tool but it is not on my camera. I will post it in the next few days that works easier on the old rotors.
So, you can bounce, compress, do what ever you prefer. But I learned along time ago that it didn't work for accuracy/less stiction. Try doing it this way once, then try the bounce, brake and compress method and see how far you are off.
Out of curiosity, my son's 08 WR 125, with the bounce, brake and compress method. It was 2mm off. It sure made a difference in the stiction free up only being off 2 mm. Being off like that has to take it's toll on the bushings and seals.
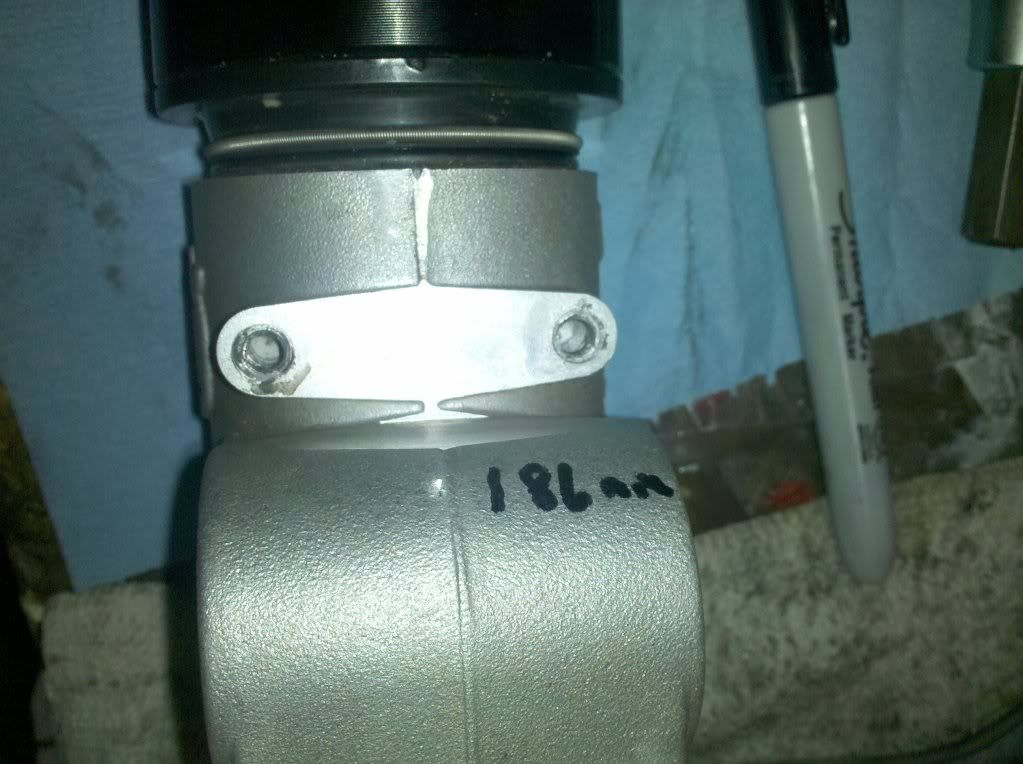